Volvo zoekt de marges in slim onderhoud
De productie van de Volvo-fabriek in Torslanda bij Gothenburg moet de komende drie jaar met 50 procent omhoog. Smalle marges en intensieve concurrentie maken een dergelijke schaalvergroting noodzakelijk.
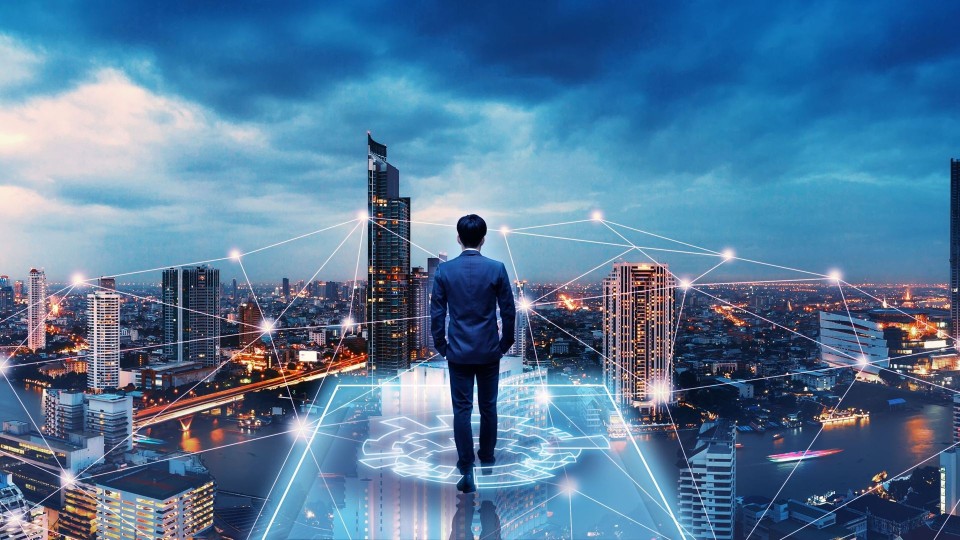
Shutterstock
Shutterstock