Sony haalt RFID uit de pilotfase
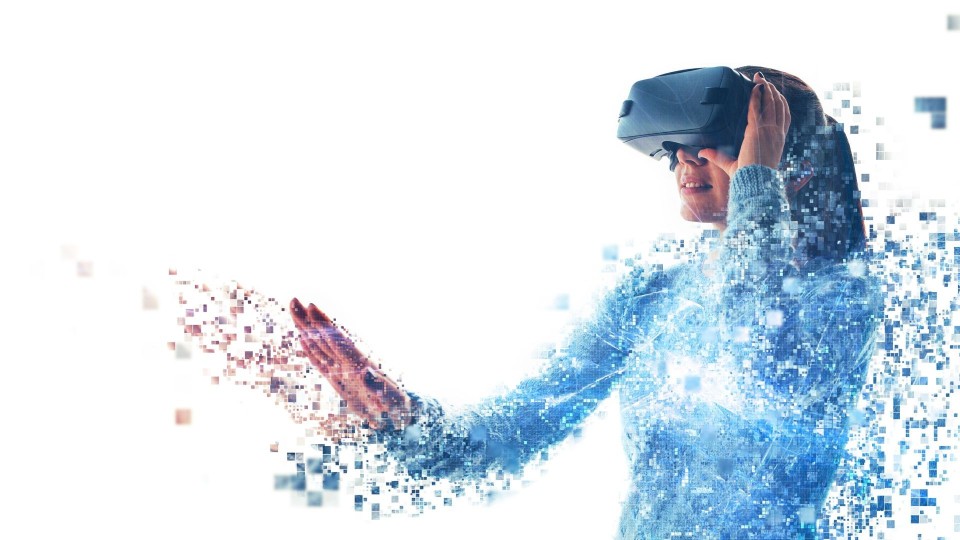
In het ‘uitgaande’ deel van dat proces werden tot voor kort de barcode-labels op de dozen met elektronica stuk voor stuk gescand door de orderpickers van dienst, om aan het centrale voorraadbeheersysteem te laten weten dat een product daadwerkelijk richting afnemer onderweg was. Dat scannen gebeurt voortaan met RFID-apparatuur, die op verschillende plekken de dozen en de pallets waarop ze staan signaleren. De barcodelabels zijn er nog steeds en zien er hetzelfde uit, maar bevatten nu een RFID-label, dat bij het printen dezelfde nummercode meekrijgt.
Testen
Al in 2004 begon Sony met het testen van RFID-technologie van de eerste generatie, om ervaring op te doen, maar ook om erachter te komen dat de verwachte voordelen nog niet gerealiseerd konden worden. De Gen2-chips en bijbehorende uitleesapparatuur die in 2006 beschikbaar kwamen, waren aanleiding voor het opnieuw uitproberen van de technologie − deze keer met meer perspectieven. Het snel uitlezen van een pallet vol dozen blijkt daarmee snel genoeg te kunnen.
Erg veel fysieke factoren blijken in de tests van invloed op de goede en snelle werking van RFID: het merk en soort van de chips en de apparatuur spelen een grote rol, evenals de oriëntatie van de antennes, de onderlinge afstand van de tags, de ondergrond waarop het label is geplakt, de manier waarop dozen op een pallet zijn gestapeld en ook de bandbreedte die er voor de om radiosignalen vechtende readers beschikbaar is. Maar onoverkomelijke problemen bleken er niet.
Sander Merkx, die voor RFID-systeemintegrator Mieloo & Alexander het project begeleidde, heeft wel een paar uitdagingen ervaren. “Er was honderd procent accuratesse nodig en het systeem mocht niet ingrijpen in de bestaande werkwijze.”
Video
Elke verzamelde pallet met dozen wordt ten minste drie keer gescand. Eerst worden de verschillende labels op de pallet gelezen en gecheckt tegen het aantal dozen. Op een volgend station wordt de pallet in plastic verpakt en van een palletlabel voorzien, dat in het systeem aan de dozenlabels wordt gekoppeld. Tegelijkertijd wordt dat proces op video gezet, waarbij de RFID-codes in beeld worden meegeschreven. Die beelden dienen als bewijs voor de levering als die betwist wordt. Ten slotte wordt de pallet nog eens bij de laaduitgang gescand en wederom op video gezet. De vele scans leidden in eerste instantie tot complicaties. Ten eerste pakken de talrijke antennes snel signalen op die niet voor ze bedoeld zijn en ten tweede kunnen er vanwege Europese regels slechts 10 frequentiekanalen tegelijk gebruikt worden (in de VS 50). “Je krijgt dan een fileprobleem met de signalen”, aldus Merkx. “Toen we de systemen voor het eerst aanzetten, ging de performance snel van 100 naar 0 procent.” Beide problemen zijn opgelost door voor een centraal systeem te kiezen dat alle ‘domme’ RFID-lezers beheert. Die ‘tag acquisition processor’ (TAP, een systeem van leverancier Reva) is voorzien van algoritmes waarmee het bijvoorbeeld kan herkennen op welke laaddeur een pallet afgaat, door naar de patronen in de signalen te kijken. Soms zijn ergens RFID-lezers geplaatst die vaststellen dat een pallet op een bepaald moment ergens juist níet staat. Ook het bandbreedteprobleem is centraal opgelost met prioriteringsalgoritmes in de TAP.
De TAP stuurt op zijn beurt precies dezelfde informatie door naar het SAP-voorraadbeheersysteem als voor februari, toen nog met barcodes werd gewerkt.
De accuratesse kan alsnog in het gedrang komen als de kwaliteit van de RFID-tag zelf niet goed is. De echt slechte tags worden door de labelprinter al geweigerd, maar twijfelgevallen niet. Daarom krijgen de tags aan het begin van het proces alsnog een extra signaaltest, waarbij wordt gecontroleerd hoe snel een signaal terugkomt. Als dat een fractie van een seconde te lang duurt, wordt het label alsnog vervangen. Dat is bij ongeveer 1 à 2 procent het geval. Merkx heeft uitgerekend dat in het Sony-project de prijs van een RFID-tag uitkomt op ongeveer 7 cent. Daarbovenop komt dan nog eens 11 cent per uitleesactie (‘read’).
Terugverdienen
Directeur Gerard de Witt van Sony Supply Chain Solutions stelt dat de investeringen snel terugverdiend zullen zijn. “En die besparingen halen we puur op mankracht.” Het met een handscanner lezen van alle barcodes op een verzamelpallet is beduidend arbeidsintensiever dan een eenmalige RFID-scan. In dit geval wordt het werk vooralsnog door even veel mensen gedaan, maar is het videocontrolesysteem wel binnenshuis gehaald en met het RFID-systeem geïntegreerd. Voorheen werd het videosysteem door een vervoerder voor zijn rekening genomen.
Te zijner tijd hoopt De Witt ook RFID- te kunnen inzetten voor de binnenkomende goederen. Onlangs in het in elk geval gelukt een pallet met 5 x 7 x 10 Handicams in één keer te scannen. “Zo’n pallet hoeft dan niet meer afgebroken te worden”, zegt Merkx.